某高压转子连接螺母拧紧扳手传动系统失效分析
2019-05-29
0 引言
各类机械传动系统无论是在普通的机械设备、运输工具还是航空、航天、航海等领域应用都十分广泛[1]。轴承作为支撑转动部件的关键零件,是各类机械传动系统中的重要部件,轴承服役工况复杂,对制造质量、加工装配精度、润滑质量等要求极高,又要经受摩擦热以及振动等严酷的使用环境,失效概率相对更大,失效现象和行为也更为复杂[2],实践表明,大量机械设备中传动系统的失效在很大比例上是由于轴承首先失效而引起的[3]。显然,确保轴承在各种工况下都能正常工作,对于避免传动系统发生故障具有非常重要的意义[4]。
本文对某高压转子连接螺母拧紧扳手传动系统进行了失效分析,通过现场失效信息调查,对相关故障件进行断口分析,显微组织及硬度检测,判定此次失效的肇事件及失效模式,并对失效模式特征进行阐述。
1 失效信息
某高压转子连接螺母拧紧扳手(以下简称“工装”)传动系统在拧紧螺母过程中,发生卡滞,分解后发现,齿轮齿牙发生断裂、轴承破坏。该工装传动系统自上而下主要由力矩输入齿轮、2#、3#传动齿轮和力矩输出齿轮组成,其中两个中间传动齿轮轴分别采用两个滚动轴承支撑。
该工装传动系统故障位置是力矩输入齿轮,即驱动轮,与两个中间传动齿轮,即2#齿轮和3#齿轮,其中驱动轮及与其相邻的2#齿轮各有1个齿牙断裂,3#齿轮1个齿牙变形,2#齿轮一侧轴承破坏,保持架、防尘盖脱落,部分滚珠破裂,其余3个轴承不能灵活运转,故障件外观如图1所示。各故障部位材料牌号及硬度要求如表1所示。其中,轴承类型为两面带防尘罩的深沟球轴承。
图1 故障件外观
表1 各故障部位材料及硬度要求
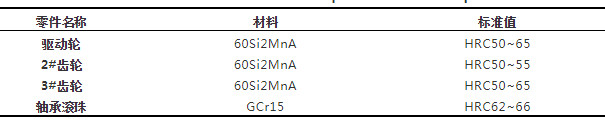
2 试验与分析
2.2驱动轮
2.2.1断口分析
驱动轮1个齿牙断裂,其它齿牙未见变形及机械损伤痕迹,驱动轮断裂齿牙断口宏观微观形貌如图2所示,驱动轮齿牙断裂位置在齿牙顶部,断口尺寸约1cm,断口宏观呈纤维状,可见棱线收敛于一侧齿根,为断裂起始区(如图标记所示),起始区未见明显材料冶金缺陷和机械损伤痕迹,断口呈现出过载断裂特征,起始区可见沿晶脆性断裂特征,扩展区呈现出典型的韧窝断裂形貌。
图2 驱动轮齿牙断口宏观微观形貌
a)断口整体;b)起始区;c)扩展区
2.2.2显微组织及硬度检测
驱动轮显微组织如图3所示,主要由回火马氏体和少量碳化物组成,未见明显异常。根据ASTME140标准中材料硬度换算表,将将驱动轮维氏硬度换算为HRC,结果分别为:57.2(672HV1)、57.6(680HV1)、57.6(680HV1),对比标准值和实测值发现,驱动轮硬度检测结果在合格区间内。
图3 驱动轮显微组织
2.3齿轮
2.3.1断口分析
2#齿轮有1个齿牙断裂,3#齿轮1个齿牙塑性变形,其它齿牙未见变形及机械损伤痕迹。2#齿轮齿断裂齿牙宏观微观形貌如图4所示,断裂位置在齿牙顶部,断口尺寸约7mm,宏观呈纤维状,可见棱线收敛于一侧齿根,为断裂起始区(如图标记所示),起始区未见明显材料冶金缺陷和机械损伤痕迹,断口呈现出过载断裂特征,起始区可见沿晶脆性断裂特征,扩展区呈现出典型的韧窝断裂形貌。3#齿轮一齿牙产生变形,系加力过程中受断裂齿轮碎块挤压所致。
图4 2#齿轮齿牙断口宏观微观形貌
a)断口整体;b)起始区;c)扩展区
2.3.2显微组织及硬度检测
在金相显微镜下观察2#、3#齿轮显微组织形貌,如图5所示,两者显微组织相似,均主要由回火马氏体和少量碳化物组成,未见明显异常。根据ASTME140标准中材料硬度换算表,将2#、3#齿轮维氏硬度换算为HRC,结果如表2所示。对比标准值和实测值发现,3#齿轮硬度检测结果在合格区间内,2#齿轮硬度略超出上限。
表2 齿轮硬度检测结果
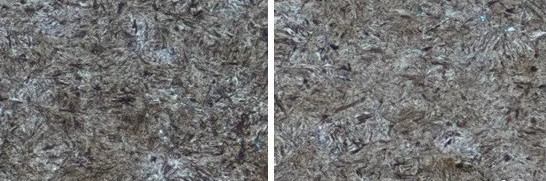
图5 齿轮显微组织
a)2#齿轮;b)3#齿轮
2.4轴承组件
2#齿轮的1个轴承破坏,滚珠破裂、保持架变形、脱扣,滚道挤压损伤,端盖脱落变形。放大镜观察轴承内部有黄油,未见黄油结块硬化、结焦及明显异物进入。
2.4.1滚珠
1)滚珠断口分析
2个滚珠断口宏观微观形貌如图6所示,断口表面比较粗糙,呈纤维状,局部有磨损;1#滚珠断口可见棱线收敛于滚珠表面与中心,故存在两个断裂起始区,断裂先在滚珠表面起始,后在中心起始,而后汇聚,产生台阶;2#滚珠断裂主源位于中心,边缘多个周向次生脆断区,台阶特征不明显。1#滚珠断口起源于滚珠表面缺口处,裂纹从表面向滚珠心部扩展,表层裂纹的出现,使得滚珠受力不均,心部受到大载荷作用,产生二次裂纹源,表层起源裂纹扩展过程中遇到心部起源的裂纹后两者汇合,形成台阶状断口;2#滚珠断裂主源位于中心,边缘有多个周向次生脆断区,说明2#滚珠受力更大,在高载荷作用下,多处起裂,形成心部放射状主要过载断口特征;两滚珠心部及表层起始区均有不同程度的沿晶脆性断裂特征,扩展区均呈现出典型的韧窝断裂形貌。
图6 滚珠断口宏观微观形貌
a)1#滚珠断口整体b);2#滚珠断口整体;c)滚珠断口起始区;d)滚珠断口扩展区
2)滚珠显微组织及硬度检测
在金相显微镜下观察滚珠显微组织形貌,如图7所示,主要由回火马氏体和碳化物组成,未见明显异常。根据ASTME140标准中材料硬度换算表,将滚珠维氏硬度换算成HRC,结果分别为:67.3(941HV1)、67.2(937HV1)、66.9(928HV1),对比标准值和实测值发现,滚珠硬度略超出上限。
图7 滚珠显微组织
2.4.2保持架
该轴承采用浪式带扣保持架,保持架宏观形貌如图8a所示,从图中可以看出,该保持架兜孔大小不一,已产生严重变形,搭扣部位发生错位,且部分保持架搭扣已经脱开,失去对滚珠的约束作用。
拆解2#齿轮未破坏轴承,该轴承滚珠完好,滚珠及内外滚道表面有轻微划伤,保持架有变形,且两半保持架的搭扣部位有明显错位,如图8b所示。
图8 保持架
a)已破坏轴承保持架兜孔变形及脱扣;b)完整轴承保持架搭扣错位
2.4.3轴承滚道
轴承内滚道表面存在滚珠局部挤压痕迹及划伤,挤压损伤不在滚道中心,偏向一侧,表明滚珠已偏离预定的运行轨道,受力局部化,导致滚珠局部受力增大,划伤系滚珠碎块受力接触滚道所致,如图9所示;轴承外圈侧面局部产生挤压损伤,系保持架变形,滚珠碎块脱落受轴承座挤压所致。
图9 轴承内滚道表面挤压及划伤
3 综合分析与讨论
3.1肇事件分析
综合上述试验结果,扳手传动机构失效主要是驱动轮、2#齿轮断裂、3#齿轮变形及轴承破坏。失效结果是传动机构卡滞。其中驱动轮和2#齿轮断齿,2#齿轮1个轴承破坏,3#齿轮1齿变形,其余3个轴承运行不灵活、力矩输出齿轮完好。机构中损伤Z为严重者为驱动轮与2#齿轮,因此3#齿轮和力矩输出齿轮不是本次失效肇事件。
驱动轮和2#齿轮均有1个齿牙断裂,两处断口均为过载断裂,断裂起始区未见材料冶金缺陷及明显加工损伤,其余部位也未见卡滞损伤,因此齿轮直接卡滞导致机构运转卡滞的可能被排除,也就是说,驱动轮和2#齿轮齿牙断裂不是本次失效的原因,而是机构卡滞后,较大的拧紧力矩输入引起的过载断裂,断口起始部位均存在不同程度的沿晶断裂特征,这与几种材料高硬度及表面化学处理有一定关联,并非材料缺陷。因此2#齿轮处发生破坏的轴承是本次失效的肇事件。
3.2失效原因分析
破坏轴承由内外滚道、保持架、滚珠、上下防尘盖构成。根据轴承组件结构及分析结果看,上下防尘盖仅有密封作用,即使破坏,也仅仅是防尘盖脱落,并不能影响滚珠的运动,因而轴承破坏与防尘盖无关。宏观观察轴承内部有黄油,未见黄油结块硬化、结焦及明显异物进入,且滚珠与滚道之间没有摩擦痕迹,说明轴承润滑良好,可排除润滑不良引起轴承损坏的可能。内外滚道仅有少量挤压损伤及划伤,无明显变形,也不是造成轴承破坏的肇事件。轴承多个滚珠出现过载断裂,而滚珠的组织正常,硬度略超上限,滚珠要想破裂,须有超过断裂强度(GCr15断裂强度约2155-2550MPa[5])的应力方可发生,若滚珠在预定的轨道运转,不可能产生这么高的应力。轴承内滚道表面存在滚珠局部挤压损伤和划伤痕迹,说明滚珠存在偏离预定的运行轨道的情况,当滚珠偏离预定轨道时,受力局部化,可导致局部应力异常增高,这为滚珠的破裂提供了应力条件。由此可知,滚珠过载破裂并非材料冶金缺陷引起,而是滚珠偏离预定轨道导致应力异常所致,也就是说,滚珠偏离轨道在先,破裂在后,滚珠不是轴承破坏的肇事件。因此,轴承保持架是本次轴承失效的肇事件,破坏轴承保持架变形、脱扣,运转不灵活轴承保持架错位变形是保持架肇事的直接证据。
轴承保持架功能主要是约束滚珠的位置,使其均匀分布,并引导滚珠在正确的轨道上运行。本次轴承的保持架为浪式带扣结构,由两个对称的浪式结构通过一侧保持架自带的锁紧边通过弯曲锁紧的方式连接,而不是传统的铆接等连接方式,而且锁紧开口方向一致,没有实现反向互锁,这种单侧锁紧方式不能有效锁紧保持架。在轴承装配过程中或工作承受冲击载荷时,两半保持架易于错位,甚至脱开,其错位或者脱开都会引起滚珠位置偏离。当保持架错位较小时,滚珠能够灵活运转,一旦个别错位偏大,滚珠位置偏离,则保持架就会承受附加应力,发生变形,进而加剧滚珠位置偏离,直至破坏。
综上所述,本次工装传动系统失效的主要肇事件为发生破坏的2#齿轮轴承。其余零件断裂、变形或损伤均属二次损伤。当单侧锁紧的浪带式带扣保持架在装配或工作承受冲击载荷时,易于错位、变形,甚至脱扣,并引导滚珠偏离预定轨道,造成滚珠破裂,轴承破坏,进而导致系统运转卡滞、断齿失效。
4 结论
1)驱动轮和2#齿轮齿牙断口为过载断裂,起始区呈沿晶脆性断裂,扩展区呈典型韧窝断裂;
2)轴承滚珠断口为点源或线源起始的过载断裂,局部呈沿晶脆性断裂,扩展区呈典型韧窝断裂;
3)发生破坏的2#齿轮轴承是本次失效的肇事件;
4)轴承单侧锁紧的浪式带扣保持架在装配或工作过程中,受到冲击载荷,搭扣错位变形、脱扣,致使滚珠偏离预定的运转轨道,造成滚珠过载断裂,引起轴承破坏,进而导致该工装传动系统卡滞、断齿失效。