薄壁内齿套渗碳淬火变形后如何处理?
2020-03-29
张殿龙,杨晓红
(泰尔重工股份有限公司)
我公司生产的鼓形齿联轴器产品为钢铁企业各轧制生产线上必备的传动部件,用在电机和减速机之间或减速机与设备之间,本次研究对象为减速机与轧辊之间的主传动接轴,该接轴传递转矩大,靠内齿套与外齿套齿部配合传递扭矩。选用17CrNiMo6低碳合金钢制造,采用渗碳淬火工艺,使齿面具有高的耐磨性,心部具有良好的韧性,保证产品在线使用寿命至少15个月。
由图1和图2可以看出,整个内齿套包括内齿及外花键厚度在内28mm左右,属于典型的薄壁工件。因此,渗碳淬火变形控制为该内齿套制造的难点。本文通过对内齿套采用渗碳+感应淬火及渗碳+等温淬火两种工艺进行研究,解决了该内齿套淬火变形的问题。
1.内齿套技术要求及热处理工艺
内齿套的内孔为模数7、44,要求内齿套通过渗碳淬火齿面有效硬化层深度≥2.5mm,齿面硬度58~62HRC。外圆分布116个模数为3的花键,要求外花键表面硬度不能超过35HRC。
由图示1上的标注的具体尺寸可以看出,齿侧及齿根与外齿配合面,光洁度要求0.8μm,齿顶为非接触面,光洁度无要求,只需满足公差要求,故齿侧及齿根渗碳淬火后需要磨齿机进行磨削达到图纸要求的光洁度,齿顶在渗碳淬火数控车至图样要求的尺寸,渗碳淬火后不需要加工。渗碳淬火前内齿侧及齿根单边留有0.4mm余量,若齿侧及齿根余量加大,表面渗碳淬火层中硬度和近表面良好金相组织将会被加工掉,并且会造成磨齿机的效率降低,成本增加。若渗碳淬火整个热处理变形超过0.4mm,即后序磨齿无法加工。
本文以齿顶的尺寸测量数据为基准,对渗碳前及渗碳后、淬火后进行尺寸跟踪测量,根据齿顶的尺寸判定渗碳淬火后整个齿圈的变形量是否符合后序磨齿的要求。
2.采用渗碳+感应淬火工艺
工艺流程如下:锻(正火)→粗车→去应力回火→半精车→插内齿→渗碳→感应淬火→精车外圆→端面→磨内齿(齿侧、齿根) →插外花键→成品。
渗碳前加工图如图3所示,与成品图对比,外圆余量5mm,渗碳为整体渗碳,工艺曲线见图5。渗碳后对齿部进行单齿淬火,采用中频设备功率280kW,为了保证齿部两侧及齿底硬度,感应器做成齿槽型如图4所示,对44个内齿依次进行中频感应淬火。
感应淬火后硬度检测结果符合图纸的技术要求。对内齿齿顶尺寸φ296.8H7采用内径千分尺进尺寸检测,数据如表1所示:由尺寸检测结果可以看出,10件工件内孔整体均呈现向外胀的趋势,胀大量在0.4~0.6mm,齿侧后序无法进行磨齿满足Z终成品的尺寸要求,零件全部报废。此内齿套渗碳后齿面为高碳合金成分,采用中频单齿淬火,组织转变时产生的组织应力及热应力导致工件外胀变形,另外工件心部及其他部位未进行淬火,强度低,内应力超过基体的屈服强度引起工件外胀变形超差而报废。
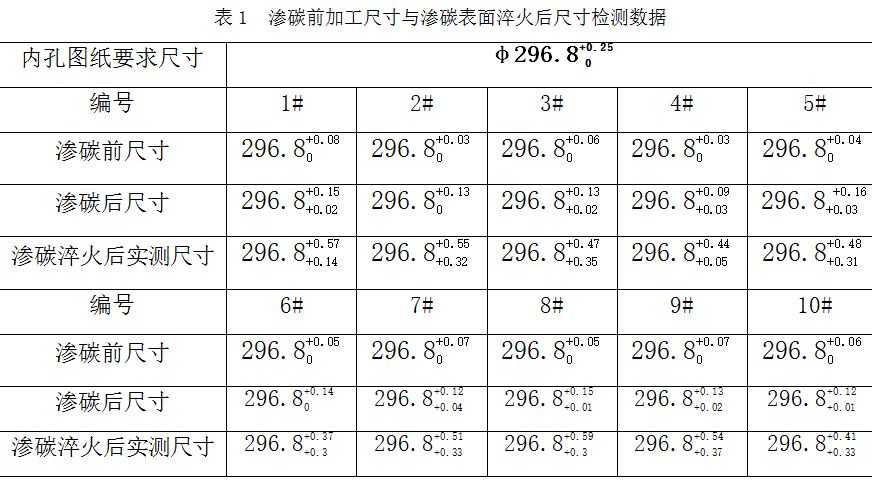
3.渗碳+等温淬火
工艺流程中除感应淬火改为等温淬火外,其余工序相同。渗碳工艺按照原来的工艺执行,渗碳前在内齿以外的部位刷防渗碳涂料,防止渗碳淬火后外圆及端面加工困难。淬火使用多用炉加热,氮气保护,工件单层直接摆放淬火吊架,不能挤压及叠加装炉。淬火冷却根据等温淬火的原理,冷却介质为好富顿MT355等温淬火油,此淬火油在Ms点附件具有缓慢的冷却速度,可以有效的缓解组织应力及热应力引起的变形。
对比渗碳前工件的加工尺寸与渗碳等温淬火后工件的尺寸,可以看出,等温淬火内齿齿顶小径尺寸变形控制在0.25mm以内,满足齿顶公差尺寸及齿侧、齿根所留的磨量0.4mm;齿部以外部位渗碳时刷了防渗碳涂料,淬火后硬度检测结果在31~34HRC,符合要求的35HRC以内,不影响后续外花键的加工。
4.结语
薄壁件渗碳淬火,工艺采用感应淬火满足齿部的硬度要求,但由于组织转变时产生的组织应力及热应力导致工件外胀变形无法控制;通过改进淬火工艺,渗碳后采用等温淬火,齿部变形量符合磨量的要求,没有废品产生,具有一定的经济效益。
(来源:热处理生态圈)